- Strona główna
- -
- Aktualności
- -
- Implementing tire and wheel handling systems – sounds like a piece of cake, right? It’s not.
Implementing tire and wheel handling systems – sounds like a piece of cake, right? It’s not.
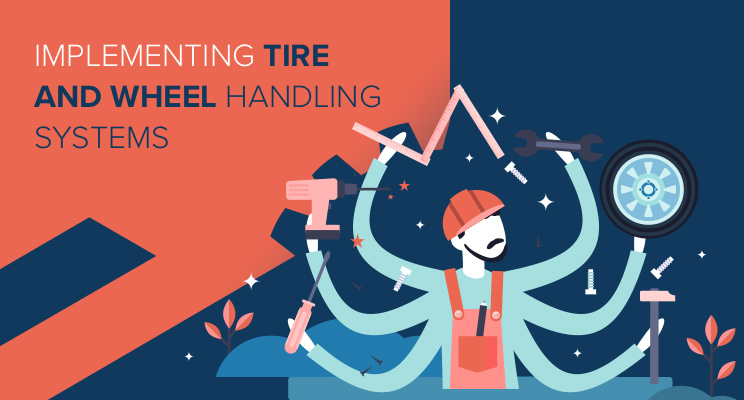
The wrong type of conveyors, a tire sticking to the line, a system that doesn’t take into account the efficiency of employees, inadequate software calibration, are just some of the things that can go wrong when transporting tires. Krzysztof Bieniek, Head of Technical Department from Transsystem explains how to prepare for the implementation of such solutions and how to properly manage the risks.
When analysing different systems used in production or transport, we usually focus on the competitive advantages and benefits of a specific solution. However, manufacturers rarely speak directly about the risks associated with the system’s implementation. So, what can go wrong?
The main problem is the lack of an individual approach to customer needs. Many manufacturers use off-the-peg solutions and then try to adapt them to the specifics of a given company. However, this isn’t always possible. An example is the use of conveyors with non-standard lengths, e.g., 1.75 meters or 2.18 meters, which is caused, for example, by the distance to the hall wall, to the machine or other issues. In such situations, many companies impose an obligation on the customer to incorporate such a conveyor so that it can be used in the factory.
But shouldn’t the range of existing solutions be the basis for preparing a transport system project? Relying on a ready-to-go product will definitely shorten the process of preparing the proposition and its implementation.
Well, in actual fact, it is completely the opposite because our experience shows that it is a tailor-made solution that allows us to quickly conduct such a project. The whole process is based on measurements carried out in the customer’s factory with the participation of steelwork and mechanical engineers, safety specialists, an electrical engineer and a software developer, who can precisely determine the type of conveyors of the transport system at individual stages of the line: green tires (intermediate product – rubber may stick to a different surface at this stage), curing (collection from presses), final finishing and palletizing. In addition to technical aspects, the team also obtains information about the performance of the machines used, production capacity, as well as the number of tires that are produced and the length of all other operational times.
All of this sounds complicated and suggests it is a time-consuming task.
And in fact, it is. However, because of the extensive know-how of our team, of the experience which we have gained from over 300 projects, and meticulously gathered data, we are able to prepare an offer in just 2-3 weeks.
This is a relatively short time, taking into account all aspects that need to be considered when designing such a solution.
Yes but there are many of them. These are, for example, the types of conveyors that I mentioned earlier. Often there is a situation when the supplier mistakenly assumes that a traditional conveyor belt should be used, which may simply not fulfil its role. At this point, it is worth mentioning that green tires may stick to either the line or to the next green tire if they are not properly separated during transport. In such a situation, the employee has to waste time on detaching the tire, slowing down the entire transport process and causing the company to miss its targets for the day. And in the case of final finishing, we have to properly predict the number of tires to be buffered, e.g., for visual inspection stands points. However, thanks to measurements and detailed interviews with potential customers, we know how much time the operator needs to make such an inspection. We know how many tires leave the line. On this basis, we design the whole system in such a way that people at the inspection points are able to manage their tasks.
The human factor in the transport process is crucial.
Of course, that’s why the company responsible for the preparation and implementation of the system must understand every aspect of work from a client’s team. Imagine that at the system design stage, the company doesn’t consider that since the barcode is placed only on one side of the tire, you need to consider whether it is definitely on the same side that the barcode is scanning. If someone doesn’t foresee this, then additional optimizations will have to be made: turning the tyres or placing the scanner in a different position. Reading the barcode is an essential step in production. Eventually, the tires are automatically divided into those that are sent to car factories (OE) and those intended for the aftermarket (RE). An additional challenge which recently appeared on the market is QR-code engraving on each tire. This process must also be foreseen during process planning with additional conveyor technology being required by the plants for QR coding.
So the preparation and implementation of the system is then mostly risk management. Am I right?
Potential risk, because predicting the problems translates into the efficiency of the whole system, resulting in the customer smoothly and successfully implementing the whole transport process. However, first of all, we have to check whether a potential solution would in reality work. And again, the extensive range of solutions offered by Transsystem is of paramount importance here. During the selection of conveyors for the project and the analysis of a company’s commercial needs, software developers check to see if the designed solution is feasible. At this stage, for example, an additional buffering intervention may be needed at a certain stage or it may be necessary to require the mechanical engineer to change the concept of the project. Expectations do not always go hand in hand with reality. We had a customer, a global manufacturer, who asked a different supplier to design a system for green tire storage. Fortunately, we visited the plant beforehand to make the measurements for this storage area’s construction, and as it turned out, the equipment was too high and had to be redesigned. Our client simply overlooked this issue.
And there is also the entire infrastructure of the factory.
That’s right. Transport systems are designed for brownfield and greenfield factories. The former is much more challenging because they are already operating facilities, equipped with specific machines, with designated passageways, etc. In this case, the design of a new tire transport structure must take into account any mismatches or any other problems that may occur within the existing infrastructure. It is also important to consider the fact that people and vehicles should have the possibility to move with ease on the production site. And when it turns out that some element of the tire transport system needs to be affixed to the roof, it is necessary to calculate the permissible load on a specific section of the ceiling to ensure the absolute safety of workers.
Okay, but creating a whole transport system is a process in which it’s not only the customer and the company responsible for designing and implementing the solution that take part.
Yes, because we still have to consider component suppliers for the entire system. Many companies cede this obligation to the customer. This leads to a number of potential risks, which is why we focus on cooperation with a selected group of belt or roller suppliers for tire factories, and they know which types can be used in particular transport areas. Some of these suppliers even develop special compounds, types of belts or rollers, upon request, to guarantee a standard that meets a particular company’s needs.
And how quickly are you able to implement such a project?
Direct cooperation with suppliers allows us to significantly shorten the time of project implementation, even in the case of very high standards. The extensive specialization of our company, our know-how, and competent team allow us to carry out the complete process in 8-16 weeks, which compares favourably to an industry average of 20 weeks plus.
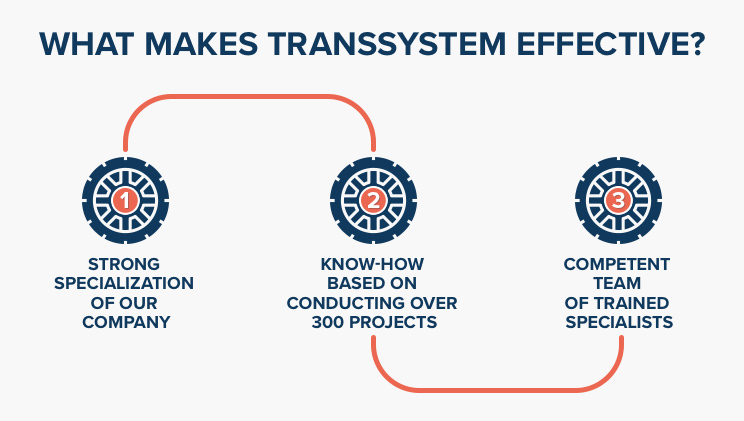
We have already touched upon the human factor that can generate potential problems. However, there are also technologies that have to be considered.
Of course. The tire transport system also includes robotics solutions. This is the case, for example, during the palletization stage. A common problem here is the centring of the tire on the conveyor. It can’t be moved to the right or left because the margin for error is really small. In the curing stage, on the other hand, it is the synchronization of the tires that counts. The presses have two rows, and the tires are placed next to each other. This requires proper calibrating so that the correct spacing between the tires is maintained. If the software is poorly prepared, the tires may start to bump into each other, leading to delays in production.
How can we avoid that?
It is necessary to be familiar with Rockwell Automation, Siemens or Mitsubishi software, which are used by a particular supplier. That is why our team includes specialists who are trained in supplier companies – they have access to the latest industry recommendations and tech innovations. However, we have to analyse some things ourselves and configure the system in such way that the comfort of maintenance service employees is maintained. After all, they are responsible for the continuity of production and are a key element in the process.
Transsystem specializes in designing and manufacturing material handling systems suited to the needs of its customers. The company has gained experience by implementing projects in many countries, in the vast majority of tire and car factories around the world as well as other industrial sectors.
If you want to discuss what solutions would be the best for your company, contact us: https://transsystem.pl/en/contact/
To learn more about Transsystem’s offer, please go to: https://transsystem.pl/en/offer/transportation-of-tires-wheels-and-rims/